製造現場の整理・整頓術 – 5Sの基本とポイントを解説!
2024.04.06

製造現場の片隅に、使用済みの部材や古い治工具が積み上がっています。生産ラインの脇には、不要な書類や図面が散乱し、目的のものを見つけ出すのにひと苦労です。こうした光景は、多くの中小製造業の現場で見られるものではないでしょうか。
生産効率を上げ、納期を守るためには、整理整頓は欠かせません。しかし、日々の業務に追われ、なかなか手が付けられないのが実情です。
「整理整頓は大切だと分かっているが、何から始めればいいのか分からない」
「一度は整理したものの、すぐに元に戻ってしまう」
このような悩みを抱えている経営者や現場リーダーも多いのではないでしょうか。
整理整頓は、5Sの基本であり、現場の安全性や品質の向上にも直結する重要な活動です。しかし、その取り組み方や定着させるためのポイントを知らないがために、なかなか前進できないでいる現場も少なくありません。本記事では、整理整頓の重要性を再確認し、具体的な進め方やコツについて解説していきます。
目次
なぜ整理・整頓が必要なのか?
整理整頓は、単に現場をきれいに保つだけではありません。それは、生産性の向上や品質の安定、安全性の確保など、製造現場の様々な課題解決に直結する重要な活動なのです。
第一に、整理整頓は生産性の向上に大きく寄与します。必要なものがすぐに取り出せる状態になっていれば、無駄な時間や動作を削減できます。また、適切な場所に適切な量の部材や工具が配置されていれば、手待ち時間も最小限に抑えられるでしょう。
第二に、整理整頓は品質の安定にも貢献します。整理された現場では、不良品や不具合の発生を早期に発見しやすくなります。また、部材や工具の管理が徹底されていれば、混入や取り違えのリスクも減らせます。
第三に、整理整頓は安全性の向上にも不可欠です。整理された現場では、つまずきや転倒などの事故リスクが減ります。また、整理整頓をすることで避難経路がわかりやすくなり、万一の災害時でも従業員の安全を確保することにつながります。
さらに、整理整頓は、従業員のモチベーションや職場環境の改善にも効果があります。整然とした現場は、従業員の誇りややる気を高め、コミュニケーションを円滑にします。
このように、整理整頓は、生産性、品質、安全性、モチベーションなど、あらゆる面で現場力を高める原動力となります。中小製造業が競争力を維持・強化するためには、整理整頓の重要性を再認識し、社員全員が日々の業務の中で取り組む必要があるでしょう。
整理・整頓が進まない根本的な原因は?
整理整頓の重要性は理解できても、なかなか実践できない現場が多いのが現状です。その根本的な原因は何でしょうか。
まず挙げられるのが、「現場の習慣や意識の問題」です。「今までこうやってきたから」「忙しくて整理している時間がない」といった意識が、整理整頓を阻む大きな要因となっています。
次に、「リーダーシップの不足」も問題です。現場の管理者自身が整理整頓の重要性を十分に理解していなかったり、率先して行動を示せていなかったりすると、現場の意識改革は進みません。
また、「整理整頓の方法やルールが明確でない」ことも、取り組みが進まない原因の一つです。何をどこまですればいいのか、基準が曖昧では、現場は混乱してしまいます。
加えて、「整理整頓の習慣が定着していない」ことも大きな問題です。一時的な整理だけでは、すぐに元の状態に戻ってしまいます。継続的な活動として定着させる仕組みづくりが不可欠なのです。
最後に、「整理整頓の効果が実感できない」ことも、モチベーションの維持を難しくしています。目に見える形で成果を示し、現場の努力を認めていくことが重要です。
これらの根本的な原因を一つ一つ解決していくことが、整理整頓を進める上での鍵となります。現場の意識改革、明確なルール作り、継続的な取り組み、効果の可視化など、多角的なアプローチが求められるでしょう。
5Sについて

5Sとは、「整理」「整頓」「清掃」「清潔」「しつけ」の頭文字を取ったもので、製造現場の効率化と質の向上を目指す活動の基本となるものです。この5つの要素を継続的に実践することで、現場の安全性、生産性、品質を高めることができます。
5Sは、単なる整理整頓ではありません。それは、現場の問題点を発見し、改善につなげるための重要な手法なのです。5Sを通じて、ムダな作業や動線、不良品の発生源などを明らかにし、改善のPDCAサイクルを回していくことが求められます。
また、5Sは、現場の従業員一人ひとりの意識改革と、チームワークの向上にも大きな効果があります。全員が5Sの意義を理解し、自ら主体的に取り組むことで、現場の一体感とモチベーションが高まっていきます。
5Sの要素
5Sの具体的な要素は、以下の通りです。
1. 整理(Seiri):不要なものを取り除き、必要なものだけを残す
2. 整頓(Seiton):必要なものを使いやすく配置し、すぐに取り出せる状態にする
3. 清掃(Seisou):設備や作業場を清潔に保ち、ごみや汚れがない状態にする
4. 清潔(Seiketsu):整理、整頓、清掃した状態を維持し、職場の衛生管理を徹底する
5. しつけ(Shitsuke):決められたルールやマニュアルを遵守し、5Sを習慣づける
これらの5つの要素を、PDCAサイクルを回しながら継続的に実践していくことが、5Sの本質です。一時的な活動ではなく、日常の業務の中に5Sを組み込み、現場の文化として根付かせていくことが重要なのです。
5Sは、中小製造業の現場力向上のための強力な武器となります。その本質を理解し、全社一丸となって取り組むことが、競争力強化につながるでしょう。
整理・整頓の具体的な進め方の3つのポイント
5Sの第一歩である整理・整頓を進めるためには、具体的な手順と基準が必要です。ここでは、整理・整頓の進め方について、3つのポイントを解説します。
①不要なものの判断基準と処分方法
現場に散乱する物の中には、「将来使うかもしれない」と思って残しているものも多いでしょう。しかし、それらは生産活動の妨げになるだけでなく、スペースの無駄遣いにもつながります。
不要なものを判断する基準としては、たとえば「過去1年間使用していないもの」「今後1年間使用する予定のないもの」が挙げられます。これらに該当するものは、処分を検討しましょう。
②必要なものの分類と保管場所の決め方
現場で使用する部材や工具、書類などは、用途や頻度に応じて分類し、最適な場所に保管することが重要です。
分類の基準としては、「毎日使うもの」「週に1回使うもの」「月に1回使うもの」などが考えられます。これらを踏まえて、使用頻度の高いものは手の届く範囲に、低いものは少し離れた場所に保管するなど、メリハリをつけることが大切です。また、保管場所を決めて関係者に周知したり、保管場所に置く工具名のラベルを貼ったりするなど、誰でもすぐに分かるような工夫が必要でしょう。
③現場の意見を取り入れる
最後に、「現場の意見を取り入れる重要性」を強調したいと思います。整理・整頓の基準やルールは、現場の実情に合ったものでなければ、定着しません。
現場の従業員一人ひとりが、自分の仕事に必要なものは何か、どこに保管するのが最適かを考え、提案できる機会を設けることが重要です。現場の意見を吸い上げ、それを整理・整頓の計画に反映させることで、現場の主体性とモチベーションが高まるでしょう。
これらの3つのポイントを踏まえて、整理・整頓を進めていくことが求められます。現場の実態に合った基準とルールを設定し、全員の参画を得ながら、一歩一歩着実に実行していくことが成功の鍵となるでしょう。
整理・整頓を習慣づけるための3つのポイント
整理・整頓を一時的なイベントで終わらせず、現場の習慣として定着させるためには、いくつかのポイントを押さえておく必要があります。
①ルールと可視化
整理・整頓の基準ややり方をルールで明文化し、現場の隅々まで浸透させることが重要です。ルールを目に見える形で掲示したり、手順書やマニュアルを作成したりすることで、誰もが確認できる状態にしておきましょう。
また、整理・整頓の状態を可視化することも効果的です。写真や動画を使って、「あるべき状態」を明示することで、現場の従業員が目指すべきゴールを共有できます。
②定期的な確認と改善
整理・整頓の状態を定期的にチェックし、問題点を洗い出して改善につなげる仕組みが必要です。
具体的には、5Sパトロールを実施したり、5S監査のためのチェックリストを作成したりすることが考えられます。これらを通じて、現場の状態を客観的に評価し、改善のためのアクションプランを立てていきましょう。
③全員参加の仕組みづくり
整理・整頓は全員が行うような仕組みにしましょう。特定の人だけの仕事にしてしまっては、その人が退職してしまった後は現場の状況は改善前に逆戻りしてしまうでしょう。これでは、整理・整頓が現場に根付いたとは言えません。
全ての従業員が主体的に取り組むための仕掛けが必要です。例えば、5S提案制度を設けて、現場からのアイデアを吸い上げたり、5S表彰制度を導入して、優れた取り組みを称賛したりすることが効果的でしょう。また、5S活動を日々の業務の中に組み込むために、社員の目標管理に記載することも一案でしょう。
これらのポイントを踏まえて、整理・整頓を現場の文化として醸成していくことが求められます。ルールの明確化、定期的なモニタリング、全員参加の体制づくりなどを通じて、5Sを組織の DNA に刻み込んでいくことが、中小製造業の現場力向上につながるでしょう。
整理・整頓をはじめとする5S活動は、一朝一夕には定着しません。しかし、地道な努力を積み重ねることで、必ず現場は変わっていきます。5Sを通じて、現場の意識改革と継続的改善の文化を築いていくことが、中小製造業の競争力強化の鍵となるのです。
5Sの効果と限界
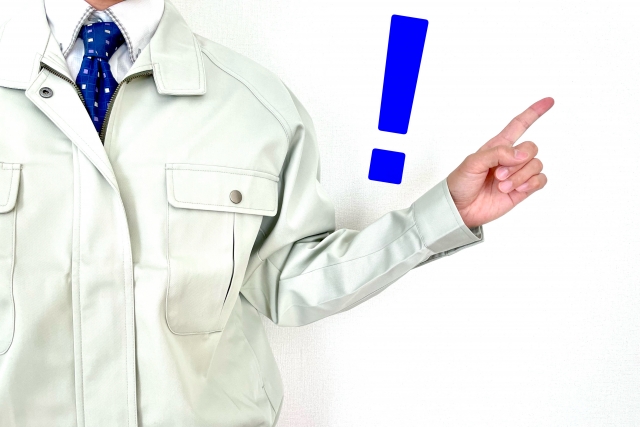
5Sは、製造現場の効率化と質の向上に大きく寄与する手法ですが、その効果と限界についても理解しておく必要があります。
5Sによって得られるメリット
まず、5Sを実践することで得られるメリットは多岐にわたります。
第一に、生産性の向上が挙げられます。整理・整頓された現場では、無駄な動作や探す手間が削減され、作業効率が大幅に改善されます。そのため、作業者は製造・加工業務に集中することができ、結果的に不良品の発生を減らすことにつながるでしょう。
第二に、品質の安定化も期待できます。整理・整頓・清掃を徹底することで、不具合の早期発見と対処が可能になります。また、作業の標準化が進むことで、製品のバラつきも抑えられるでしょう。
第三に、安全性の向上も見逃せません。整理・整頓された現場では、事故やケガのリスクが大幅に減少します。また、非常時の避難経路の確保にもつながります。
さらに、従業員のモラルやモチベーションの向上、5S活動によるコミュニケーションの活性化など、職場環境の改善効果も期待できます。
5Sだけでは解決できない問題
その一方で、5Sだけでは解決できない課題もあることを認識しておくことが重要です。
例えば、設備の老朽化や技術力不足、原材料の品質問題など、5Sの範疇を超える課題があります。これらについては、設備投資や人材育成、サプライヤーマネジメントなど、別の施策を併せて実施する必要があるでしょう。
また、5Sは、あくまでも現場の改善活動の一つであり、経営戦略や事業計画とは異なるレベルの取り組みです。5Sを実践することは重要ですが、それだけで企業の競争力が高まるわけではありません。
5Sを土台として、技術力の向上や新製品の開発、営業力の強化など、様々な経営施策を総合的に展開していくことが求められます。
このように、5Sの効果と限界を正しく理解することが、活動を成功に導く上で欠かせません。5Sのメリットを最大限に引き出しつつ、その限界を補完するための施策を同時に進めていくことが、中小製造業の現場力向上につながるでしょう。
5Sは、現場改善の強力な武器ですが、万能薬ではありません。その特性を踏まえた上で、経営戦略の一環として位置づけ、推進していくことが重要だと言えます。
5Sの次のステップ
5Sの取り組みを進め、現場の整理・整頓が習慣化してくると、次のステップとして、図面の管理方法を見直すことが有効です。中でも、図面の電子化と一元管理は、製造現場の効率化と品質向上に大きく寄与します。
図面の電子化
まず、図面の電子化についてですが、これは紙の図面をデジタルデータに変換することを指します。CADソフトで作成された図面データを活用することで、様々なメリットが得られます。ここでは、「図面と検索と共有が容易になる」「図面の保管スペースを削減できる」の2点のメリットを挙げたいと思います。
第一のメリットは、図面の検索と共有が容易になることです。必要な図面をキーワードで瞬時に検索できるようになり、現場でも設計部門でも、最新の図面にアクセスできるようになります。
第二のメリットは、図面の保管スペースを削減できることです。電子化した図面はサーバーやクラウドで保存されるため、紙の図面を保管していた図面棚が不要となります。社内のスペースが増え、社内のオフィス環境の改善につながります。
電子化した図面の一元管理の重要性
図面を電子化しただけでは、図面管理は十分とは言えません。電子化した図面を一元管理することが、真の効果を発揮するための鍵となります。
図面は、設計部門だけでなく、製造、調達、品質管理など、様々な部門で使われます。これらを一つのシステムで管理することで、部門間の情報共有とコラボレーションが飛躍的に向上するのです。
例えば、設計変更があった場合、その情報が即座に現場に伝わり、製造の手順書や検査基準にも反映されます。また、図面と連動した部品表を管理することで、購買部門の調達ミスを防ぐことができるでしょう。
このように、図面の電子化と一元管理は、製造現場の効率化と品質向上に直結するテーマです。5Sの先の課題として、ぜひ検討していただきたいと思います。
その際、クラウド型の図面管理システムの活用も視野に入れてみてください。自社サーバーを構築することなく、低コストで導入できるのがメリットです。例えば、「図面バンク」では、月額26,000円で利用を開始でき、電子化された図面の一元管理を容易に実現できます。
「電子化されたファイルは見づらく、一目で探したい図面が分かりにくい……」とお思いの方もいるかもしれません。
図面バンクの図面一覧画面では、下図のように図面のプレビューが大きく表示され、Windowsのエクスプローラ画面で見るよりも見やすくなっています。この機能により、探したい図面が見た目で分かりやすくなっています。

5Sの次のステップとして、図面の電子化と一元管理に取り組むことで、中小製造業の現場力は、さらに大きく向上するはずです。デジタル技術を味方につけ、競争力の高い製造現場を実現していきましょう。
まとめ
本記事では、中小製造業の現場力向上に欠かせない「5S」について、その重要性と具体的な進め方を解説してきました。
5Sは、製造現場の基本中の基本であり、生産性、品質、安全性など、あらゆる面で現場の体質を改善する上で欠かせない取り組みです。特に、「整理」と「整頓」は、5Sの中でも最も重要な要素であり、まずはここから着実に進めていくことが大切だと言えます。
整理・整頓を進める上では、不要なものの判断基準と処分方法、必要なものの分類と保管場所の決め方など、具体的な手順を明確にすることが求められます。また、現場の意見を取り入れ、全員参加で取り組む体制を構築することも重要なポイントです。
5Sの取り組みを習慣化するためには、ルールの明文化と可視化、定期的な確認と改善、全員参加の仕組みづくりなどが欠かせません。地道な努力を積み重ねることで、5Sを現場の文化として根付かせていくことができるでしょう。
さらに、5Sの次のステップとして、図面の電子化と一元管理にも着手することをおすすめします。紙の図面をデジタルデータ化し、クラウド上で一元管理することで、現場の効率化と品質向上を大きく前進させることができます。
その際、「図面バンク」のようなクラウド図面管理システムの活用を検討してみてはいかがでしょうか。低コストで導入でき、図面一覧時のプレビューが見やすく、初めて図面管理システムを使う方でも使いやすいツールになっています。
無料トライアルもご用意していますので、ぜひ一度お試しいただければと思います。
5Sと図面の電子化・一元管理は、中小製造業の現場力向上に欠かせない取り組みと言えます。デジタル技術を味方につけ、競争力の高い製造現場を実現していきましょう。